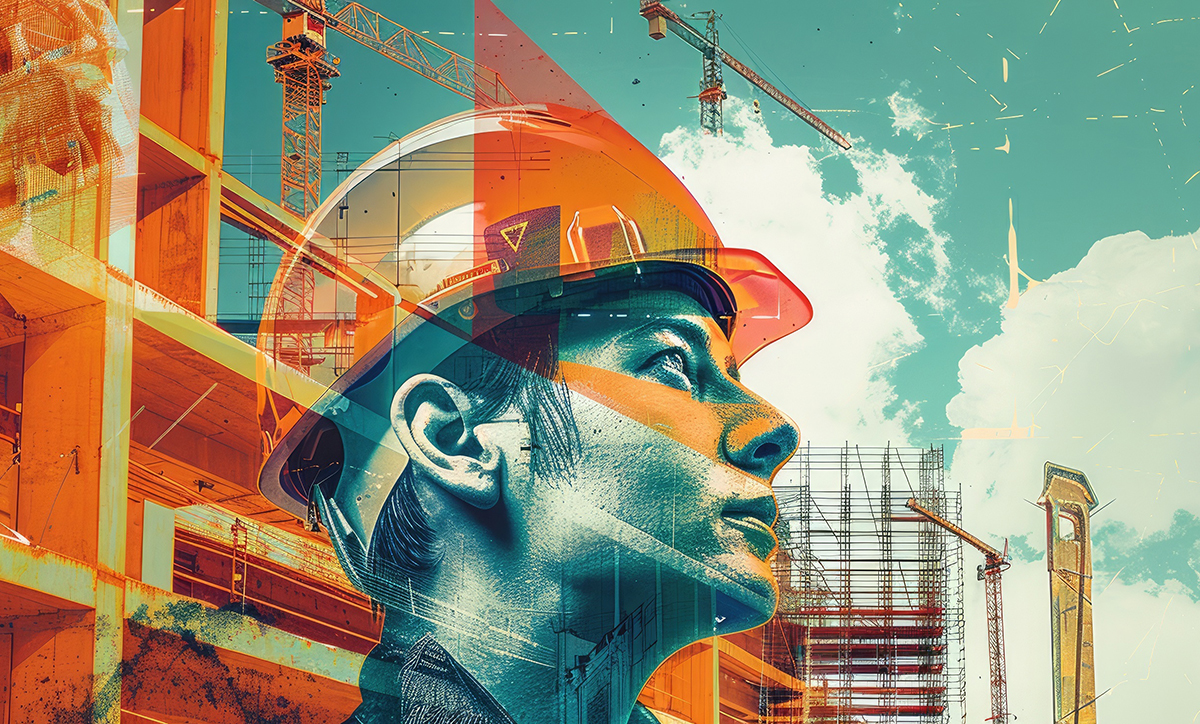
Cost Escalation in Australia's Building and Construction Industry
The building and construction industry in Australia is experiencing a significant challenge that affects everyone from developers to homeowners: cost escalation.
According to corporate watchdog ASIC, there were 2832 construction industry insolvency appointments for the 2024 financial year until June 16, an increase of 28 per cent on the 2213 insolvencies over the previous financial year. The construction sector remains by far the single largest category of insolvency. See Financial Review article “nearly 3000 building companies go broke in a year”
This is the fourth item of a 10-part shortlist from Back to Basics previous blog “There is no quick fix for the Australian housing problem” on addressing the housing shortage in Australia.
We previously identified the following
- Issue: Rising material costs, fluctuating labor costs, and increased regulatory requirements contribute to overall project cost escalation.
- Impact: This can strain project budgets, reduce profit margins, and make projects financially challenging to complete.
We need to understand cost escalation before we can offer some strategies that can help.
Understanding Cost Escalation
Cost escalation refers to the gradual increase in the cost of construction projects over time. This can be attributed to various factors, including inflation, changes in labour costs, and fluctuations in the prices of materials. In Australian, these factors are compounded by unique local conditions and market dynamics.
“Since 2019 we have seen the cost of home building increase by 40 per cent. The delivery of new homes and related infrastructure has been obstructed by ongoing and concurrent challenges.
“Tradie shortages, planning and licensing delays, draconian industrial relations changes, material cost inflation, inefficient regulation, unfeasible lending practices and risk allocation are compounded to make projects unsustainable.” - Master Builders Australia CEO Denita Wawn source news.com.au
Key Drivers of Cost Escalation
- Material Prices
One of the most visible drivers of cost escalation is the fluctuation in material prices. Recent years have seen substantial increases in the cost of essential construction materials such as steel, timber, and concrete. These price hikes are often driven by supply chain disruptions, increased demand, and global economic conditions. For instance, the COVID-19 pandemic significantly disrupted global supply chains, leading to shortages and inflated prices for many materials.
- Labour Costs
Labour costs in the construction industry have also been rising. This is due to a combination of factors including increased demand for skilled labour, changes in labour laws, and a shortage of skilled workers. In Australia, the construction industry faces a shortage of skilled tradespeople, which drives up wages and contributes to overall cost increases.
- Regulatory Changes
Regulatory changes and compliance requirements can impact costs significantly. In Australia, stringent building codes and environmental regulations often lead to increased costs for compliance. While these regulations are crucial for ensuring safety and sustainability, they can add layers of complexity and expense to construction projects.
- Economic Factors
Broader economic conditions also play a role. Inflation rates affect the cost of both materials and labour. As the economy fluctuates, so do construction costs. Additionally, interest rates and economic policies can influence the cost of financing construction projects, further impacting the overall budget.
- Project Delays
Delays in construction can have a cascading effect on costs. Weather conditions, unforeseen site issues, and logistical challenges can all lead to project delays. These delays not only extend the time frame but can also increase costs due to extended labour and equipment rental times, and potential penalties for not meeting deadlines.
Strategies for Managing Cost Escalation
- Thorough Planning and Budgeting
Effective planning is key to managing cost escalation. Detailed project planning and budgeting can help identify potential cost increases early on. This includes accurate cost estimates, contingency planning, and regular budget reviews. Employing experienced project managers who can anticipate and mitigate risks is also crucial.
- Flexible Contract Structures
Flexible contract structures can provide some relief from cost escalation. For example, cost-plus contracts allow for adjustments based on actual costs, which can help manage unexpected increases. However, these contracts require careful negotiation and transparency to avoid disputes.
- Sourcing Materials Wisely
Strategic sourcing of materials can help mitigate cost increases. This might involve bulk purchasing, seeking alternative suppliers, or negotiating long-term contracts with suppliers to lock in prices. Additionally, using locally sourced materials can reduce transportation costs and potential delays.
- Investing in Technology
Technology can play a significant role in managing construction costs. Building Information Modeling (BIM) and other digital tools can improve project planning and efficiency, helping to reduce waste and avoid costly mistakes. Embracing innovative construction techniques and materials can also offer cost-saving opportunities.
- Training and Workforce Development
Addressing the skills shortage in the construction industry through training and workforce development is crucial. Investing in upskilling current workers and attracting new talent can help stabilise labour costs and improve project efficiency.
- Risk Management
Implementing a robust risk management strategy can help anticipate and mitigate potential cost increases. This includes identifying risks early, developing mitigation plans, and ensuring that all stakeholders are aware of potential challenges and their impact on costs.
Conclusion
Cost escalation in the Australian building and construction industry presents a significant challenge, but with proactive management and strategic planning, it is possible to mitigate its impact. By understanding the key drivers of cost escalation and employing effective strategies, stakeholders can navigate the complexities of rising costs and keep projects on track.
As the industry continues to evolve, staying informed about market trends, regulatory changes, and technological advancements will be essential for managing construction costs effectively. Through careful planning, flexible contracting, and investment in technology and workforce development, the industry can better navigate the challenges of cost escalation and build a more resilient future.
The key is to educate yourself. Back to Basics is a Registered Training Organisation in Australia that offers training specifically for the building and construction industry. Contact us for information on which training course is appropriate to help manage cost mitigation.